Skills and Industry 4.0 - How to Handle The Gap
- VCARE Academy
- May 4, 2021
- 7 min read
Updated: Oct 10, 2022
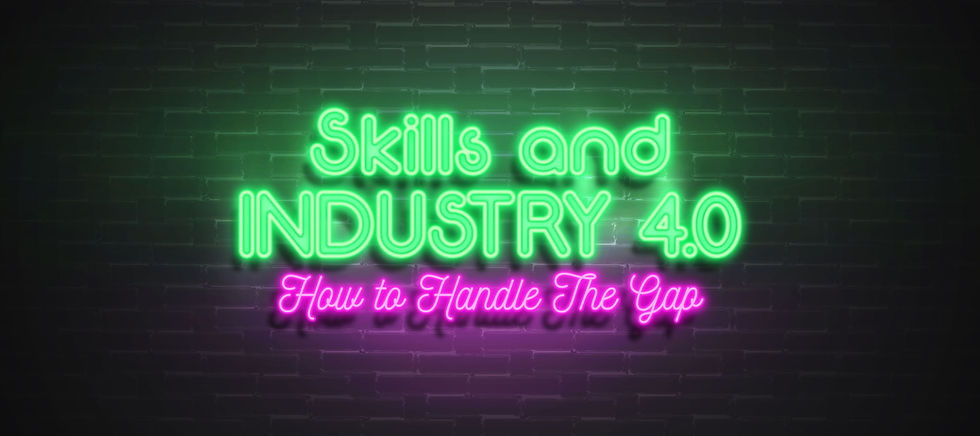
There is a strong “mismatch” of skills between supply and demand, and this does not help either the labor market or the return on investment in the industrial revolution 4.0.
The new approaches dictated by digital transformation initiatives, like Industry 4.0 and so on, are radically changing the ways of working, the human-machine-technology relationship, and the attitudes and skills required. When any geographical or national barrier is broken, competitiveness is encouraged for those capable of delivering value properly.
As any industrial transformation that took place in the past, the current one, the fourth, (after the steam engine, electricity, and information technology), seems perhaps to be the most underestimated or to have the least impact on life and work behaviors. Instead, it is known that the changes taking place over the past three to four years have actually had more impact than those that occurred in the last hundred years. It is estimated that about 65% of children who attend primary school today will have a job that does not exist today.
The substitution of labor with capital, of capital with information and information with widespread and interconnected knowledge between and within devices redistributes and redefines the concept of knowledge itself, and consequently the skills necessary to govern this new scenario.
What makes the difference is the availability of real-time information in any business environment. Think about the operators of industrial machinery: they increase productivity when they have “data in the palm of their hand” about the machine status, the order scheduling, the unpredictable events that occur daily upstream and downstream along the supply chain.
Digital transformation is different from the previous industrial transformations, for many reasons, including:
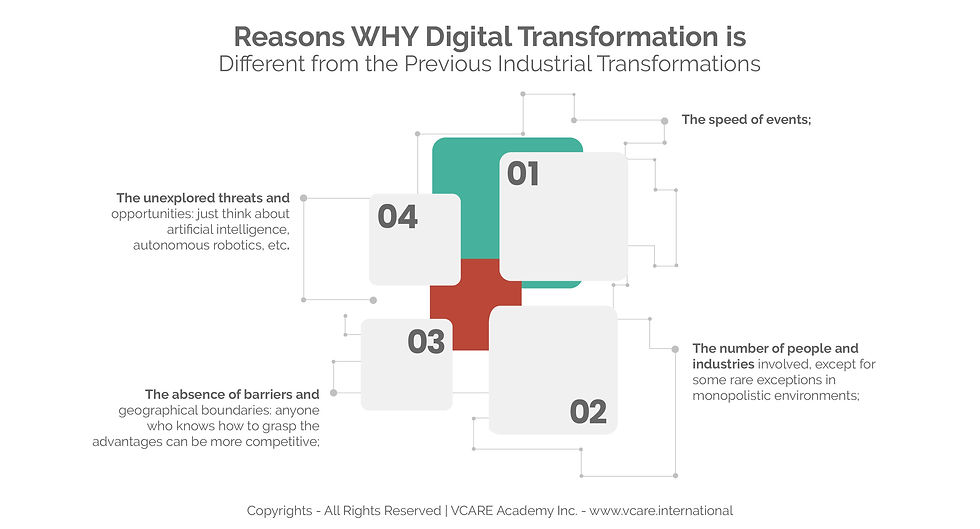
The speed of events;
The number of people and industries involved, except for some rare exceptions in monopolistic environments;
The absence of barriers and geographical boundaries: anyone who knows how to grasp the advantages can be more competitive;
The unexplored threats and opportunities: just think about artificial intelligence, autonomous robotics, etc.
Therefore, these scenarios require new efforts in innovation and re-skilling activities that have never been seen before. This is evident with the recent initiatives like those undertaken by the “World Economic Forum” (The future of jobs, 2016), the European Community (new skills agenda for Europe), and other international institutions.
THE RIGHT ATTITUDES
First, it is necessary to focus on some key attitudes to “ride” the new scenario, even before acquiring the necessary skills.

Here are some examples.
Ability to Select Data
As known, we are submerged by data, but how much of it is accurate and valid in order to help us achieve specific objectives? The ability to select, cleanse and manage data is paramount. Otherwise, we generate a huge waste of time and resources.
Ability to Adapt
Continuous changes are always part of any business scenario. Facing them with the necessary mastery and adaptability becomes essential.
Ability to Proactively Anticipate Events, Reducing Risk
The ability to perceive the evolution of events, based on trend analysis, correlations of various variables, predictive methods and so on, really help us to keep abreast and not feel overwhelmed by events. Risk management capabilities reinforce, above all, the negative impacts in manufacturing environments.
From the above considerations, we understand what skills are required, and why.
Without going into details, we can say there is a strong demand for master information adaptively.
New and high demanding job profiles are required in the operations and supply chain world.
The capability to extract value from the huge amount of data where “interconnections” are generating is key for the future of manufacturing. Think of the data obtained from social networks, the performance of the machine, the routes for movements, handling, transportation, just to name a few.
Now it is paramount to be well prepared for the coming high demand skills. Otherwise, you run the risk of losing the real benefits of the digital transformation, to make products and services more market/user-friendly and cheaper. The decrease of the “traditional” workforce, unavoidable in every industrial revolution, needs to be compensated by the increase of the “non-traditional” workforce, if the educational system (technical high schools, specialized business schools, etc.) masters the introduction of the new skills; for example, introducing some methods such as the “flipped classroom”, which puts the user of the knowledge transfer in the middle, thus using multimedia and innovative methodologies, which encourages active and interactive participation.
THE SKILLS
We start with soft skills.
Teamwork and negotiation, for example, are no longer considered among the most important skills.
On the other hand, critical thinking is gaining importance as a top skill; this consideration implies that repetitive activities will be automated in the medium to long-term. Or rather, creativity is fundamental to obtaining a systemic and overall vision of complexity; complexity needs to be recognized in order to surf within it, developing – as a consequence – strong capacities of collective intelligence, in order to face new challenges, reducing the exposure to risks.
The required hard skills have a common matrix, known as “STEM” disciplines (Science, Technology, Engineering, Mathematics).
A comparison could help in this sense. At the beginning of the ‘80s the introduction of personal computers began to generate the so-called “digital divide”: those people who could use, at least basically, a personal computer had access to many new professions. After thirty years it seems odd to meet someone who does not have a basic familiarity with a keyboard.
Now the effort is much more important: one is required to have basic skills in computer science, data analysis, and automation, or better, to be able to master not only computers, but automatic machines, to extract significant information from a large amount of data, to manage predictive maintenance, to connect/disconnect devices to the internet, and so on.
The processing power, now widespread through various types of applications, has completely changed the so-called “ecosystem”: the environment where individuals, businesses, and institutions operate.
The above increases the awareness that today, the required effort is much more important and consistent, compared to thirty years ago when information systems were introduced. Maybe these new skills, within the next ten years, will become common to many individuals, but now the speed of propagation of new technologies is exponential compared to the past, what’s new is a “technological acceleration.”
We really need to:
Continuously learn in order to find new and solid references;
Select in what domain to be an expert; and
Understand how to face the technological transformation through the ability to adapt.
This acceleration has already changed many manufacturing environments without the awareness of the professionals involved (see picking automation practices, devices for manufacturing execution systems, etc.)
It is a warning to those who wish to slow down these transformations through resistance to change and bureaucracy. But history has taught us that this attitude is a loser. It is a matter of pushing and promoting virtuous behaviors. An example is the application of the “blockchain” technology where, for example, due to common and decentralized databases, complex administrative and commercial transactions can be carried out almost in real time (for example, the management of the letters of credit that they pass from a month to a few hours).
Some of them are traditional, such as statistics or standard operating procedures, but many are new, like the example in the following table.

Big data analysis and management
Machine learning
Man-machine integration
Artificial intelligence
Predictive maintenance
Process optimization
Cybersecurity
Real-time simulations
ENABLING TECHNOLOGIES
Digital transformation, which started in Germany in 2011, is affecting most developed countries.
It is based on key enabling technologies (KET), some of them are big data analytics, augmented reality, the internet of things (IoT), simulation, etc.
At a glance, it looks like a collection of technologies, but behind each of them, there is a world of applications and solutions whose true potential is not yet known.
Think about the unexplored potential of artificial intelligence, and the impact it will have on work organization. In order to make any implementation project successful, it is important to build a digital strategy before investing.
The information flow, therefore, is no longer sequential as previously known, but runs at real time in both directions, from the customer to the supplier and vice versa throughout the supply chain, or rather the same device exchanges and stores information between other devices and the internet.
You can imagine how this scenario completely changes the meaning of generating and managing knowledge, starting from data and information, and how the required skills change accordingly.
The following question arises spontaneously: are we ready? I would say no.
We are less ready than the previous industrial revolution 3.0, the information technology of the ’70s and ’80s.
Now this change requires, above all, a knowledge of the functionalities and potential deriving from the interaction between different enabling technologies, when the development of unexplored functionalities and applications is still unpredictable but fascinating.
These technologies are, of course, tools to solve increasingly complex problems and to make everyday life more efficient and productive.
FINAL CONSIDERATIONS
The described scenario shows the urgent need to readjust and enrich the skills that are part of each person’s cultural baggage.
There is a strong “mismatch” of skills between supply and demand, and this does not help either the labor market or the return on investment in the industrial revolution 4.0.
This mismatch should be reduced step by step, and the first step is acquiring basic skills to familiarize yourself with tools and techniques now generally available to everybody, such as big data analysis, neuroscience, machine learning, and so on. It is an activity that, if carried out with a scientific method, allows one to realign valuable job profiles that are today at risk of obsolescence.
It is a “transformation acceleration” that requires above all, banishing wasted time on bureaucratic issues, realigning technical high schools, company academies, and so on.
For example, companies need an effective organizational project that goes through the following steps:

Analysis of the company’s basic processes (customer order, procurement, etc.), to highlight the most significant activities in a supplier-customer relationship;
Choice of the needed skills to execute the activities;
Correlation of the identified skills to specific job profiles;
Comparison of the skills (and their level) currently held by individuals, against those needed to better perform the activities; and
Reduction of the eventually identified gaps through targeted training or educational development plan.
This approach gets “the right person in the right place at the right time,” making the whole organization more productive. New skills are required to sustain the competitive advantage driven by the digital transformation, starting now with manufacturing.
Presented By
Ing. Giuseppe Lovecchio
CPIM-F, CSCP-F, CLTD-F, SCOR-P, DDLP, DDPP, AEFP, PMP, CSCTA, CMC, IASSC-CGB, CSSC, CPIA
Member, Education and Research Executive Board (EREB)
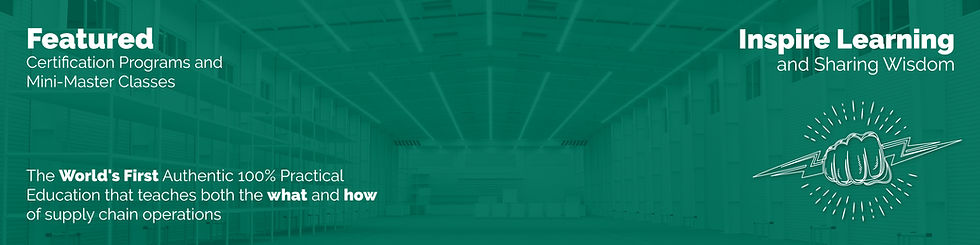
A successful career in supply chain necessitates a never-ending thirst for knowledge and the most up-to-date supply chain skills and knowledge. Even though continuing education and certification programs can take time and money, they help get your specialized knowledge or skills recognized.
When professionals have training that other professionals lack, it distinguishes them and sets them apart from the crowd. Certification and master classes show that the professionals are committed to learning, excelling, and using best practices.
Featured Certification Programs
Certified Stores and Stock Controller (CSSC)
Featured Mini-Master Classes
Featured Mini-Master Classes
Supply Chain Framework and Strategy
Collaboration among Sustainability, Procurement and Supply Chain
Implementing 3PL and 4PL Strategies in the Value Chain
Supply Chain Sustainability with Circularity to Drive Profitability
Kommentare